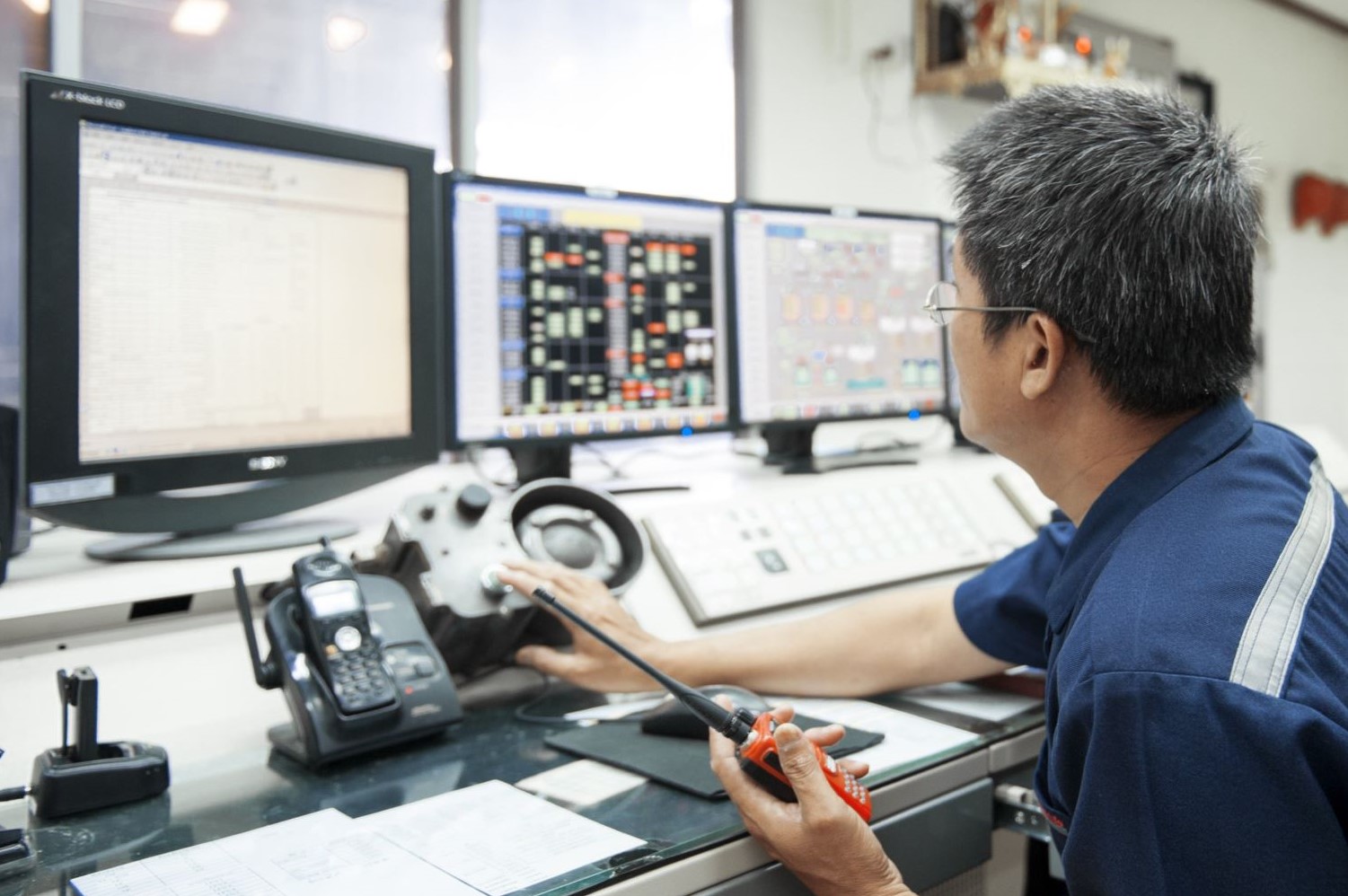
In case you hadn’t heard, Australia, along with the rest of the world, is staring down the barrel of a major supply chain predicament. The International Chamber of Shipping, along with the International Air Transport Association, the International Road Transport Union and the International Transport Workers’ Federation, has warned industry groups of an impending ‘global transport system collapse’.
But that’s not the only challenge for manufacturers and their buyers right now. Power and microchip shortages are causing issues to fulfilment well before transport becomes a concern.
So, why is this relevant to your connectivity needs? Standard timelines for delivery and deployment are off the table, with current timeframes being 3-4 times the usual. To ensure you have the connectivity, and relevant hardware, at the right price for your next project you need to plan ahead. Anyone advising you on the contrary is not being realistic.
What’s causing the problem and why does it affect connectivity?
There are several contributing factors impacting the end-to-end supply chain process, pretty much all of which can be attributed to (surprise, surprise) COVID-19. The first is the well-publicised microchip shortage. The shortage is in part caused by reduced manufacturing manpower, a raw materials shortage and power shortages impacting production. At the other end of the spectrum, there has been increasing demand from end users. The pandemic has applied pressure at each end of the process.
To add insult to injury, an already fragile freight industry faced further setbacks with the Suez Canal blockage. This exacerbated the situation considerably and the industry has not yet had time to fully recover.
The culmination of all of these manufacturing and shipping variables is that in Australia (and around the world), is presenting as a delay in goods arriving impacting fulfilment capabilities.
“The level of demand is playing havoc with costs and availability across the manufacturing and freight infrastructure. An average rental fee for a shipping container is around $2,000 but at the moment demand is driving this up exponentially to costs in the region of $12,000,” explains Paul Rudd, Procurement Manager at Orion Satellite Systems.
To combat this variance and reduce the impact felt by customers, Paul and the team at Orion have been ramping up their advance ordering. However, with changes happening weekly, delivery times cited one day can’t be assumed to be correct the next.
“We have been doing our very best to forecast ahead to overcome this, but in addition to the global issues, we have the added complexity of challenges within Australia,” adds Paul.
Additional challenges within Australia
Once orders arrive in Australian Ports, imported goods face further challenges caused by internal border closures, extra biosecurity measures and reduced road transport.
Australia has always had strict biosecurity requirements but new measures around virus control has led to storage space being in greater demand along with the resources and manpower needed to manage them. This is creating a bottleneck in the process and products coming into the country are being put to the back of an ever-increasing queue for processing.
“When products finally are processed, its still not smooth sailing. Less trucks are being authorised to travel into the state due to isolation measures and rules between states with high numbers of Covid versus those without. WA in particular has held quite strong borders and a significant amount of the products Orion supplies are destined for WA,” says Paul.
With less trucks able to make the trip, they are collecting more products at more depots to make the trip worthwhile.
“A lot of our WA customers have remote sites which already take a long time to reach, place on top of that the additional stops along the way and delays are inevitable. Lighter equipment can be flown in, but the cost of air transportation and weight limits on heavier items make this a fairly restrictive option,” explains Paul.
How Orion is tackling the issue
In addition to advance planning, the Orion team is taking several steps to ensure that customers have the necessary equipment and connectivity when they need it.
“First and foremost, we are urging all customers to allow additional planning time to accommodate manufacturing and shipping delays. We are doing everything we can to plan ahead but we really need our customers to do the same at their end,” explains Paul.
Orion’s position is stronger than some thanks to the company having strong supplier diversity. This means that in the event one supplier is struggling with fulfilment, there is another option which should lessen the impact on the customer.
“Based on the information available we are expecting supply chains to stabilise early in the New Year but that doesn’t mean that we will go straight back to business as usual. Basically, if you have a project planned for the first quarter of 2022, you need to be booking in your solution and requirements now,” stresses Paul.
If you are not sure of exact timing and requirements for your next project, we encourage you to talk with the Orion solutions team.
“Even having a rough idea ahead of time will help ensure we can deliver against key timelines. We always promote planning ahead but this year it’s a necessity, not an ideal,” concludes Paul.
Contact the team to book an appointment and get ahead with planning today.